|
Marine Valves: The Unsung Heroes of Maritime Safety and Efficiency
Maritime operations rely on a complex network of systems to ensure safe, efficient, and environmentally responsible vessel performance. Among the critical components that enable these operations, marine valves are indispensable. These specialized devices control the flow of fluids—such as seawater, fuel, lubricants, and gases—throughout a ship’s systems, from propulsion and ballast management to firefighting and waste treatment. Their reliability directly impacts vessel safety, operational efficiency, and compliance with global regulations.
The Role of Marine Valves in Ship SystemsMarine valves act as the "gatekeepers" of fluid dynamics onboard ships. Their primary functions include: Fluid Control: Regulating the flow rate and direction of liquids and gases to ensure systems operate within safe parameters. Isolation: Shutting off access to specific systems during maintenance or emergencies to prevent leaks or contamination. Pressure Management: Safeguarding equipment from overpressure by releasing excess pressure when needed. Environmental Compliance: Enabling pollution prevention measures, such as managing ballast water to avoid invasive species transfer or controlling emissions via exhaust gas cleaning systems.
Without properly functioning valves, even minor malfunctions could lead to catastrophic failures, such as engine shutdowns, fires, or environmental disasters.
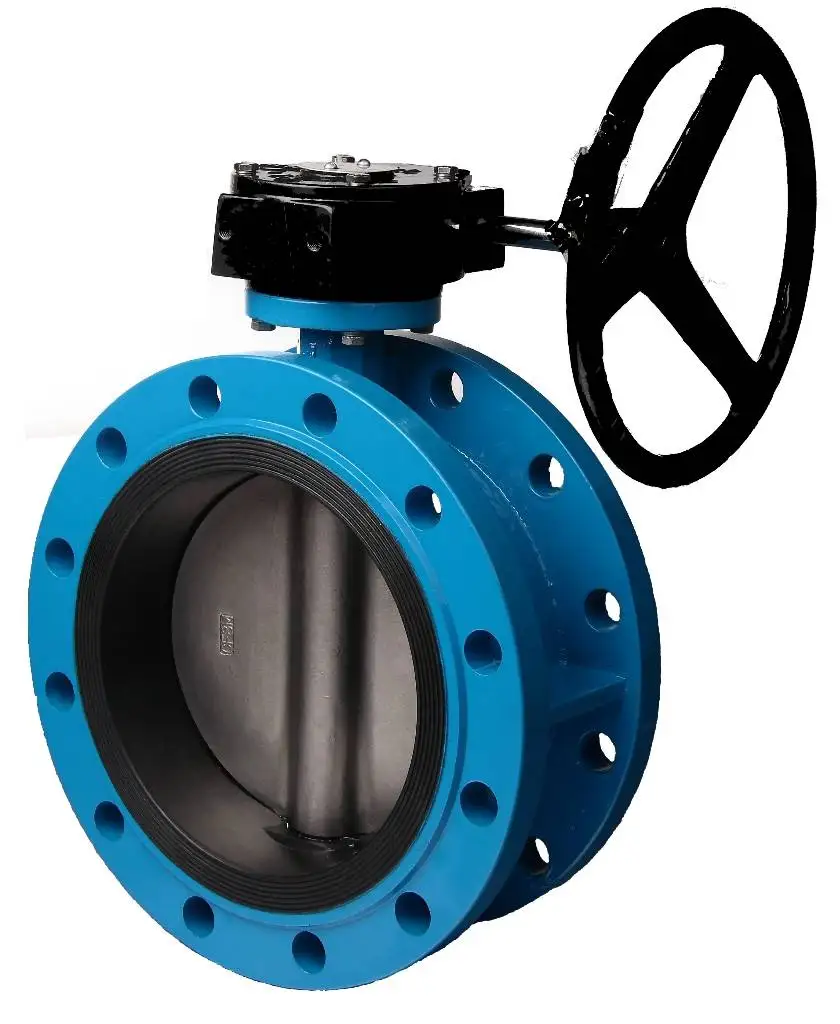
Key Types of Marine Valves and Their ApplicationsMarine valves are categorized based on design, function, and operating conditions. Below are the most common types: Gate Valves Function: Primarily used for full-flow isolation (fully open or closed). Application: Ballast water systems, fuel lines, and seawater intake due to their minimal pressure drop when open. Limitation: Not suitable for throttling or partial flow control.
Globe Valves Function: Provide precise flow regulation with a tight seal. Application: Steam systems, feedwater lines, and hydraulic circuits where controlled flow is critical. Advantage: Ideal for high-pressure applications but causes higher pressure loss.
Butterfly Valves Function: Compact design with rapid shut-off capabilities via a rotating disc. Application: Large-diameter pipelines for seawater cooling, ventilation, and cargo handling. Advantage: Lightweight and cost-effective for high-flow applications.
Ball Valves Function: Quarter-turn operation for quick shut-off and minimal resistance to flow. Application: Fuel systems, hydraulic lines, and pneumatic circuits requiring tight sealing. Material: Often made of corrosion-resistant alloys (e.g., stainless steel) for harsh marine environments.
Check Valves Function: Prevent backflow in piping systems. Application: Bilge systems, engine cooling circuits, and fire suppression lines. Critical Use: Ensures unidirectional flow to protect pumps and equipment.
Safety Valves Function: Automatically release excess pressure to prevent system overloading. Application: Boiler systems, compressed air tanks, and hydraulic accumulators. Regulatory Compliance: Mandatory in high-pressure systems to meet ISO and IMO standards.
Challenges in Marine Valve Design and MaintenanceDespite their critical role, marine valves face unique challenges: Corrosion and Erosion Exposure to seawater, chemicals, and fluctuating temperatures accelerates corrosion. Valves must be constructed from corrosion-resistant materials like stainless steel, duplex alloys, or bronze. Harsh Environmental Conditions Salt, humidity, and vibration aboard ships necessitate robust designs and regular maintenance. Regulatory Compliance The International Maritime Organization (IMO) and industry standards (e.g., ISO 15871 for ballast water valves) mandate rigorous testing and certification to ensure environmental and safety performance. Maintenance Complexity Valves in hard-to-reach areas (e.g., engine rooms) require specialized tools and trained personnel for inspection and repair.
Innovation and Future TrendsThe marine valve industry is evolving to address these challenges and meet emerging demands: Smart Valves with IoT Integration Sensors and IoT technology enable real-time monitoring of valve performance, predicting failures before they occur. For example, predictive maintenance systems can alert operators to corrosion or wear, reducing downtime. Environmentally Friendly Materials New alloys and coatings (e.g., ceramic-lined valves) are being developed to enhance durability and reduce reliance on hazardous materials. Digital Twin Technology Virtual replicas of valve systems allow engineers to simulate performance under various conditions, optimizing design and maintenance strategies. Sustainable Solutions Valves are being designed to support green shipping initiatives, such as low-emission propulsion systems and ballast water treatment technologies compliant with IMO D2 standards.
ConclusionMarine valves are the backbone of modern maritime infrastructure, ensuring safety, efficiency, and environmental responsibility at sea. As the shipping industry transitions toward sustainability and digitalization, advancements in valve technology will play a vital role in meeting these goals. By prioritizing innovation, durability, and compliance, marine valve manufacturers and operators can continue to drive progress in one of the world’s most critical industries.
|
|