|
Marine Valves: Essential Components for Naval Engineering and Oceanic Applications
Marine valves are critical components in naval engineering, designed to regulate the flow, pressure, and direction of fluids in shipboard systems. These valves must withstand harsh maritime environments, including saltwater corrosion, temperature fluctuations, and high pressure. From controlling ballast water to managing propulsion systems, marine valves ensure the safety, efficiency, and reliability of vessels. This article explores their types, applications, technological advancements, and market trends. Types and Functions of Marine ValvesMarine valves are categorized based on their design and operational requirements: Gate Valves Function: Used for full-flow or full-block applications, such as isolating pipelines. Design: Operate via a sliding gate that opens/closes vertically. Advantage: Low fluid resistance and bidirectional flow capability.
Globe Valves Function: Regulate flow rate and pressure in systems like cooling or fuel lines. Design: Feature a disc-and-seat mechanism that allows precise control. Types: Angular, Y-pattern, and straight-pattern designs for varied applications.
Check Valves Function: Prevent backflow in pipelines, critical for systems like pumps and compressors. Design: Automatically opens/closes based on fluid direction.
Ball Valves Function: Provide quick shut-off in high-pressure systems, such as hydraulic lines. Design: Rotating ball with a port for flow control. Advantage: Tight sealing and minimal pressure drop.
Safety Valves Function: Release excess pressure in boilers, compressors, or high-pressure tanks to prevent explosions. Design: Spring-loaded or pilot-operated mechanisms.
Seacock Valves Function: Intake seawater for cooling, firefighting, or ballast systems while preventing ingress of debris. Location: Installed on hulls or decks.
Subsea Valves Function: Used in deep-sea oil/gas exploration and offshore engineering. Design: Built to withstand extreme pressures (e.g., 10,000 PSI) and corrosion.
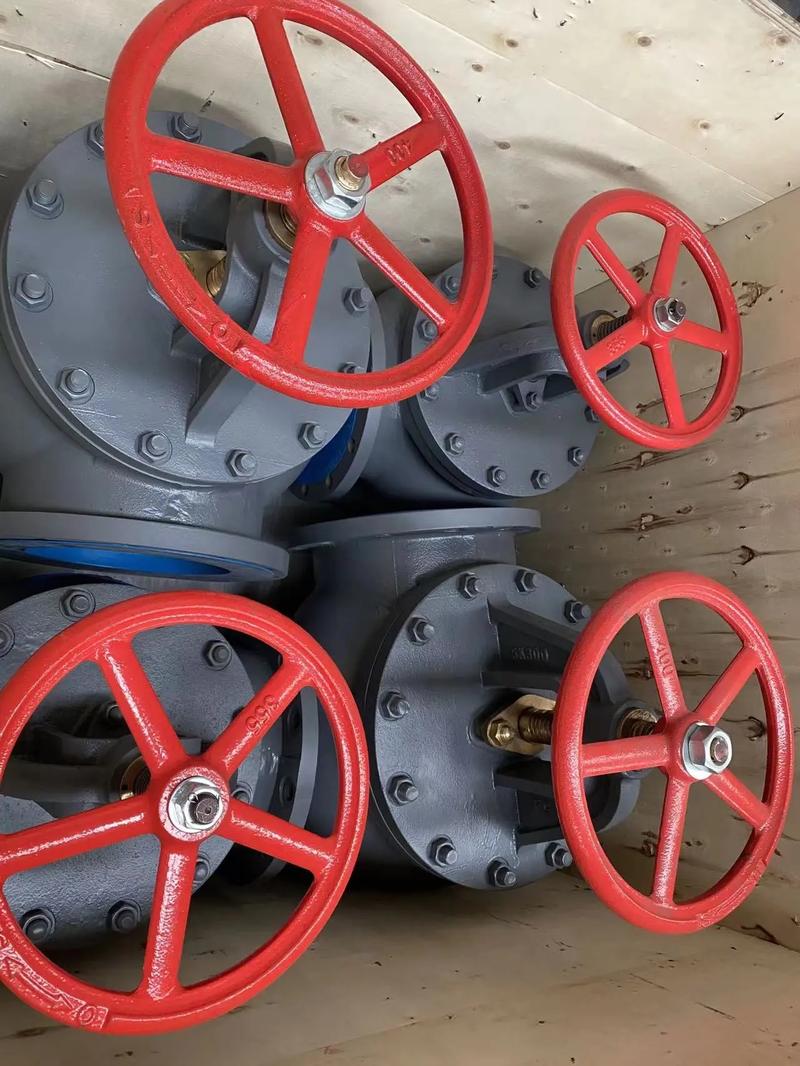
Materials and Design InnovationsMarine valves require materials that resist corrosion, fatigue, and extreme conditions: Corrosion-Resistant Materials: Stainless steel (316L), bronze, and duplex alloys are common for valve bodies and seals. Advanced Coatings: Epoxy or ceramic coatings enhance durability in harsh environments. Smart Valves: Integration of IoT sensors for real-time monitoring, predictive maintenance, and remote operation. Lightweight Solutions: Aluminum alloys reduce weight in high-capacity applications like LNG carriers.
Key ApplicationsShip Systems Offshore Engineering Subsea oil/gas extraction, underwater pipelines, and marine renewable energy (e.g., offshore wind farms).
Environmental Control
Market Trends and ChallengesGrowing Demand for Subsea Valves The global subsea valve market is projected to reach $60 billion by 2027 (CAGR of 9%), driven by deep-sea oil/gas exploration and renewable energy projects. China’s market, dominated by firms like A Company and B Company, is expanding due to rising offshore wind investments.
Technological Advancements Challenges Cost and Complexity: High-pressure subsea valves require advanced manufacturing and testing. Standardization: Ensuring compliance with international maritime standards (e.g., ISO, Lloyd’s Register).
Future OutlookThe marine valve industry is poised for sustained growth, driven by: Expansion of global shipping fleets and liquefied natural gas (LNG) carriers. Increased investment in offshore renewable energy infrastructure. Adoption of AI-driven predictive maintenance tools to optimize valve performance.
ConclusionMarine valves are indispensable for ensuring the safety and efficiency of naval and offshore systems. As technological innovation and environmental regulations evolve, manufacturers must prioritize corrosion-resistant materials, smart integration, and sustainable design to meet future demands. With the global market projected to grow significantly, advancements in this field will continue to shape the future of maritime engineering.
|
|