Marine valves are critical components in maritime systems, ensuring safe and efficient fluid control in ships, offshore platforms, and marine machinery. Designed to withstand harsh marine environments, these valves must handle saltwater corrosion, high pressure, and extreme temperatures. This guide explains valve types, applications, and selection criteria to help engineers, shipbuilders, and maintenance teams make informed decisions.
1. Common Types of Marine Valves
Understanding valve types is essential for proper application. Key categories include:
Gate Valves: Ideal for full-flow applications (e.g., seawater intake systems). Provide tight shutoff but not suitable for throttling.
Ball Valves: Offer quick on/off operation and low pressure drop. Common in hydraulic systems and fuel lines.
Butterfly Valves: Lightweight and space-efficient, used in large-diameter pipelines for flow regulation.
Check Valves: Prevent backflow in pumps and pipelines, crucial for system safety.
Safety Valves: Automatically release pressure to prevent equipment damage.
2. Key Applications of Marine Valves
Marine valves are indispensable in these critical systems:
Propulsion Systems: Control fuel, lubrication, and cooling fluids in engines.
Ballast Systems: Manage ship stability via controlled water intake/discharge.
Fire Safety Systems: Deliver firefighting water through pressure-resistant valves.
HVAC Systems: Regulate seawater for cooling in climate control units.
User Problem-Solving: Why are corrosion-resistant materials important?
Marine valves must be made of stainless steel, bronze, or duplex alloys to resist saltwater corrosion. Specify materials like ASTM A182 F51 (duplex steel) for high-pressure, corrosive environments.
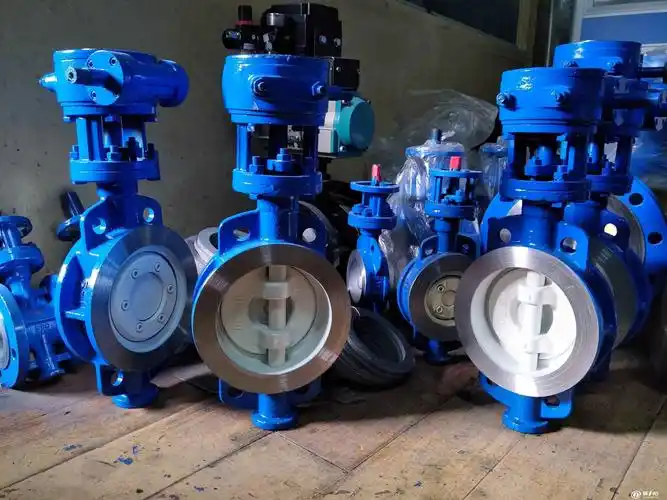
3. How to Choose the Right Marine Valve
Follow this checklist to select optimal valves:
Fluid Type: Match valve material to fluid (e.g., oil, seawater, steam).
Pressure & Temperature Ratings: Verify compliance with ISO 15812 or API 6D standards.
Space Constraints: Butterfly valves save space compared to gate valves.
Maintenance Accessibility: Prioritize valves with easy repair/replacement features.
Certifications: Ensure compliance with DNV GL, Lloyd’s Register, or ABS standards.
4. Maintenance and Troubleshooting Tips
Corrosion Prevention: Apply protective coatings (e.g., epoxy) and inspect joints quarterly.
Leakage Issues: Check gaskets and seals; replace worn components immediately.
Regular Testing: Perform pressure tests annually to ensure integrity.
Record Keeping: Document maintenance logs for audit compliance.
User Problem-Solving: What causes valve leakage?
Common causes include worn seals, incorrect installation, or sediment buildup. Use non-destructive testing (NDT) methods like ultrasonic inspection to diagnose issues.
5. Industry Standards & Compliance
Materials: Adhere to ISO 5211 (valve mounting standards).
Testing: Follow API 598 for pressure-testing protocols.
Documentation: Maintain certificates from manufacturers like KSB, Festo, or Viking Pumps.
Conclusion
Selecting the right marine valve requires balancing technical specifications, environmental demands, and compliance requirements. Prioritize quality suppliers and regular maintenance to ensure long-term reliability. For further guidance, consult marine engineering forums or whitepapers from valve manufacturers.