|
Marine Valves: Critical Infrastructure for Maritime Safety and Efficiency
Marine valves are indispensable components in naval engineering, serving as the backbone of fluid control systems on ships, offshore platforms, and subsea infrastructure. These valves are engineered to withstand the extreme conditions of maritime environments—such as saltwater corrosion, high pressure, temperature fluctuations, and mechanical stress—while ensuring reliable operation in critical applications like propulsion, ballast management, and firefighting. This article delves into the types, innovations, challenges, and future trends shaping the marine valve industry. Key Types of Marine Valves and Their Applications1. Gate ValvesFunction: Used for full-flow or full-shutoff applications in pipelines. Design: Operates via a sliding gate that blocks or opens the flow path vertically. Advantages: Minimal pressure drop, bidirectional flow compatibility, and suitability for high-pressure systems. Common Use Cases: Isolating seawater intake lines or fuel pipelines.
2. Globe ValvesFunction: Regulates flow rate and pressure in systems requiring precise control. Design: Features a disc-and-seat mechanism that allows gradual adjustment. Types: Angular globe valves (for compact installations) and Y-pattern valves (for reducing turbulence). Applications: Cooling systems, hydraulic circuits, and fuel supply lines.
3. Ball ValvesFunction: Provides rapid shut-off and control in high-pressure systems. Design: A rotating ball with a port that aligns or blocks the flow path. Advantages: Low torque operation, tight sealing, and suitability for corrosive fluids. Use Cases: Emergency shutdown systems, hydraulic pumps, and LNG carrier pipelines.
4. Check ValvesFunction: Prevents backflow in pipelines to protect pumps, compressors, and turbines. Design: Automatically opens/closes via fluid pressure. Types: Swing-check valves (for large flows) and spring-loaded check valves (for high-speed applications). Critical Applications: Cooling water systems and engine exhaust gas recirculation.
5. Safety ValvesFunction: Releases excess pressure to prevent equipment failure or explosions. Design: Spring-loaded or pilot-operated mechanisms that open at predefined pressures. Applications: Boilers, steam systems, and high-pressure storage tanks.
6. Seacock ValvesFunction: Manages seawater intake for cooling, ballast, and firefighting systems. Design: Equipped with strainers to block debris and prevent hull damage. Location: Installed on vessel hulls or decks.
7. Subsea ValvesFunction: Controls fluid flow in deep-sea oil/gas extraction and offshore renewable energy projects. Design: Built for extreme pressures (e.g., 10,000 psi) and corrosion resistance. Applications: Subsea pipelines, wellhead systems, and offshore wind turbine foundations.
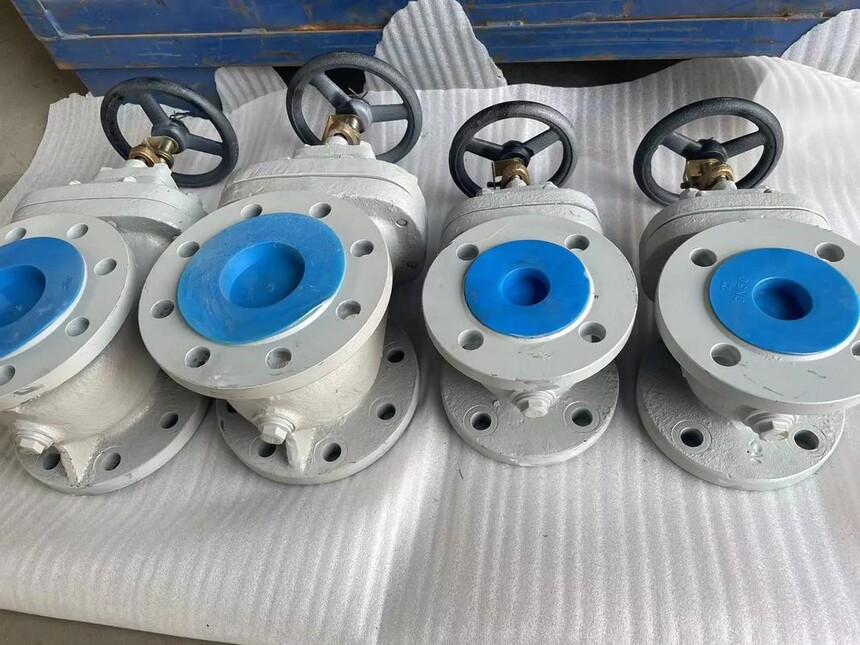
Material Innovations and Design TrendsMarine valves must balance durability, weight, and cost. Key advancements include: Corrosion-Resistant Materials: Stainless Steel (316L): Widely used for its resistance to saltwater and high temperatures. Duplex and Super Duplex Alloys: Offer superior strength-to-weight ratios for subsea applications. Nickel-Based Alloys (e.g., Monel, Inconel): Used in high-temperature or aggressive chemical environments.
Advanced Coatings: Smart Valve Technology: IoT Integration: Sensors monitor valve health, detect leaks, and enable predictive maintenance. Remote Actuation: Allows operators to control valves from shore or control rooms.
Lightweight Solutions:
Critical Applications in Maritime SystemsBallast Water Management Propulsion Systems Offshore Energy Firefighting Systems
Market Dynamics and ChallengesGrowth DriversOffshore Energy Expansion: The global subsea valve market is projected to grow at a CAGR of 8.5%, reaching $65 billion by 2030 (Grand View Research). LNG Shipping Boom: Demand for cryogenic valves in LNG carriers is rising due to increased gas exports. Environmental Regulations: Compliance with IMO’s Ballast Water Management Convention drives adoption of advanced filtration valves.
Key ChallengesHarsh Environments: Corrosion and sediment buildup in subsea systems require frequent maintenance. High Costs: Advanced materials and precision manufacturing increase upfront expenses. Regulatory Compliance: Meeting international standards (e.g., ISO 15803, DNV GL) adds complexity.
Future Innovations and OpportunitiesAI-Driven Maintenance: Machine learning algorithms predict valve failures, reducing downtime. Additive Manufacturing: 3D-printed valves enable custom designs and faster prototyping. Sustainable Materials: Biodegradable coatings and recycled alloys align with ESG goals. Hydrogen Infrastructure: Valves for hydrogen-powered ships will emerge as green shipping gains traction.
ConclusionMarine valves are pivotal to the safety, efficiency, and sustainability of maritime operations. As the industry evolves, advancements in materials, digitalization, and environmental compliance will drive innovation. With the rise of offshore energy and green shipping, the demand for robust, intelligent, and eco-friendly valves will continue to grow, positioning this sector as a cornerstone of modern naval engineering.
|
|