Marine valves are critical components in shipbuilding and marine engineering, designed to control the flow of fluids, gases, and liquids in maritime systems. These specialized valves must withstand harsh marine environments, including saltwater corrosion, pressure fluctuations, and extreme temperatures. Proper selection and maintenance of marine valves are vital for ensuring safety, efficiency, and compliance with international maritime standards. This article explores the types of marine valves, their applications, selection criteria, and maintenance best practices.
1. Types of Marine Valves and Their Functions
Marine valves come in various designs, each tailored to specific functions:
Gate Valves: Used for full-flow applications, such as opening or closing pipelines. They are ideal for non-leakage scenarios but not suitable for flow regulation.
Butterfly Valves: Lightweight and compact, butterfly valves are commonly used in water and air systems. They offer quick shut-off and are cost-effective for medium-pressure applications.
Check Valves (Non-Return Valves): Prevent backflow in pipelines, ensuring fluid moves in one direction. Essential for pumps and hydraulic systems.
Ball Valves: Provide tight sealing and are ideal for high-pressure applications. They are easy to operate and maintain.
Solenoid Valves: Electrically controlled valves used in automated systems, such as fuel and cooling circuits.
Flanged Bronze Stop Valves: Durable and corrosion-resistant, these valves are widely used in seawater systems and high-temperature applications.
Key Tip: Always specify marine-grade materials (e.g., bronze, stainless steel) to ensure resistance to saltwater corrosion.
2. Applications of Marine Valves
Marine valves are integral to multiple ship systems:
Engine Rooms: Controlling fuel, lubrication, and cooling systems.
Ballast Systems: Managing water intake and discharge to stabilize the vessel.
Fire-Fighting Systems: Ensuring rapid shut-off or activation of fire-suppression lines.
Hydraulic Systems: Regulating pressure in machinery like cranes and steering gears.
Sanitary Systems: Handling wastewater and sewage in passenger vessels.
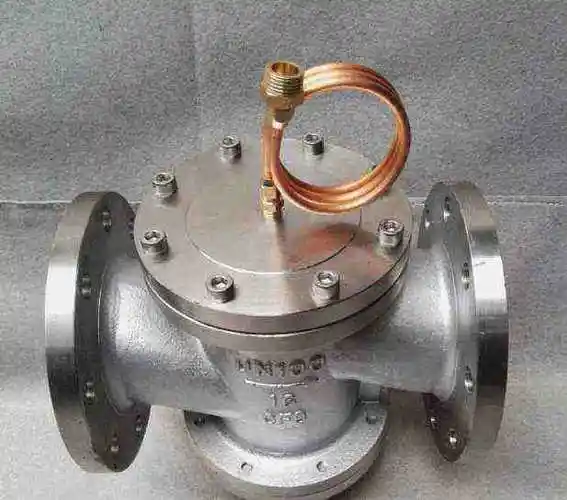
3. Key Considerations for Selecting Marine Valves
To ensure optimal performance and compliance:
Material Compatibility: Choose valves based on the fluid/medium (e.g., seawater, oil, or gas).
Pressure and Temperature Ratings: Match the valve’s specifications to the system’s operating conditions.
Certifications: Look for certifications like DNV GL, ABS, or LR for safety and reliability.
Space and Accessibility: Prioritize valves with compact designs for confined spaces.
Automation Needs: Opt for hydraulic or electric actuators if remote control is required.
4. Maintenance and Troubleshooting
Regular maintenance extends the lifespan of marine valves:
Lubrication: Apply marine-grade lubricants to moving parts to reduce friction.
Corrosion Checks: Inspect for rust or pitting, especially in saltwater-exposed areas.
Seal Integrity: Replace worn gaskets or O-rings to prevent leaks.
Testing: Conduct periodic pressure tests to ensure functionality.
Common Issues:
5. Choosing a Reliable Supplier of Marine Valves
When sourcing marine valves, prioritize suppliers with:
Industry Experience: Proven track record in maritime projects.
Custom Solutions: Ability to design valves for unique specifications.
Global Certifications: Compliance with international standards (e.g., ISO, API).
After-Sales Support: Technical assistance and spare parts availability.
Conclusion
Marine valves are indispensable for the safe and efficient operation of ships and offshore equipment. By understanding their types, applications, and maintenance requirements, engineers and operators can make informed decisions to enhance vessel performance and longevity. Partnering with certified suppliers ensures access to high-quality valves that meet the rigorous demands of marine environments.
FAQs
What is the difference between marine valves and standard industrial valves?
Marine valves are specifically engineered for corrosion resistance, pressure tolerance, and compliance with maritime regulations.
Are electric actuators suitable for all marine valves?
Yes, but ensure the actuator is waterproof and rated for marine use.
How often should marine valves be inspected?
Regular inspections are recommended every 6–12 months, depending on usage intensity.
What certifications are mandatory for marine valves?
Certifications like DNV GL, ABS, or Lloyd’s Register are critical for safety and compliance.